第五十五回。【おめんを語ろう。その四】原型編-2 「凹凸のつけ方」
-min.jpg)
お面の制作工程や、新規で発売される製品の話などを中心にお話して いく【お面を語ろう】
第四回目は、お面作りの最初の工程「原型を作る」上でのポイントの続編です。凹凸の形状のつけ方、特に塗装で着色をする前提でお面を作る場合の原型の作り方に視点を当ててお話したいと思います。
目次
彩色塗装と印刷合わせでは凹凸への考え方が全く違う。
お面の色の着け方には、スプレイガンで色を吹き着けて行く「(彩色)塗装」と印刷と形状を成形にて重ねる「印刷合わせ」とがあります。このふたつの着色方法では、原型を作る際の凹凸のつけ方にまったく異なった考え方をわたしは持っています。
塗装ならば凹凸はしっかりつける。
塗装による着色は、成形品にマスキングカバー(=塗装カバー)をあてて塗料を吹き付けることで行われます。つまり、お面の塗装には塗装カバーを用意することが必須と言えます。
理由1-切れ込みを入れる目印になる。
例えば、瞳をこげ茶に塗装するとします。その際、塗料を吹き付ける部分(=瞳)以外に塗料が着かないようにマスキングをしなくてはいけません。これが塗装カバーです。瞳の部分だけを切り抜いたカバーをかぶせて塗装をするということです。
試作や数枚の塗装の場合には成形品自体を塗装カバーにしてしまうこともありますが、大量生産用には電鋳製カバーを使います。電鋳製のカバーに関しては、またあらためてお話します。
・凹凸がカバーに切れ込みを入れる目印になる。
例えば歌舞伎の「隈取り」。あの模様は位置や形状に決まりがあって無いようなものです。汎用のものならば「おおよそこのあたり」ということで、カバーに切れ込みを入れることができます。
一方、特定の演者のお面を作るとしましょう。オリジナルの隈取りを忠実に表そうとした場合、切れ込みを入れる位置に目印がないないと職人はほとほと困ることでしょう。
理由2-吹きこぼれを少なくする。
吹付塗装は成形品にカバーをあてて行うとお話しました。この際に、成形品とカバーの間にはすき間がないことがベストです。すき間があれば、そこから塗料が外に逃げて輪郭線がボケてしまうからです。現場ではこれを「吹きこぼれ」と呼んでいます。
・握力だけでカバーをかぶせている。
対象物に塗装カバーを機械的にかぶせる方法があります。てこの原理やエアーの力を利用して機械的に密接させます。しかしわたしが知る限り、「夜店の」と呼ばれるお面の塗装にこのような機械的仕組みを使っている現場はありません。費用がかかり過ぎるからです。
残念ながら、お面の塗装にかけられる費用は約50年前とほとんど変わっていません。初期費用としてそこまで塗装カバーに費用をかけられないのです。それは工賃しかり。「機械にセットして塗装して外して」では全く生産量が上がらず、実際は握力だけでカバーをあてているのが実情です。
・人の握力だけではすき間を防げない。
真空成形で作られるお面。真空成形は「加熱と大気」で行われるシンプルな成形方法です。
シンプルなだけに他の成形方法に比べ「初期費用が抑えられる」などのメリットがあるのですが、一方「精度にバラツキが出る」というデメリットもあります。そのため、1枚の成形物から反転作った電鋳カバーとではぴったり合わないものが出てきます。
加えて真空成形に使うプラ材は「硬質」なために、ある程度の力で上から抑えつけただけでは追従しません。そのため、イメージ上ではすき間は出ないはずでも実際はほぼすき間が生じます。
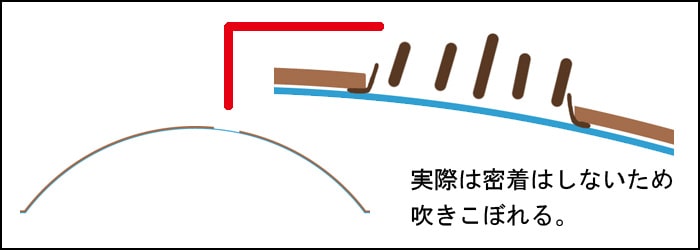
先程の隈取りの話に戻って、顔の一部に模様を一本入れるとします。凹凸は入れず、つるつるの顔に模様の形状に切り込みを入れたカバーを親指と残りの指ではさんで被せます。そして塗料を吹き付けたとすると、出方の大小はありますが吹きこぼれがまず出ます。
・吹きこぼれることを前提に目立たない形状を原型で作る。
ならば、吹きこぼれることを前提として目立たない形状を原型で作っておけということになります。具体的には以下のイメージのようなことを考えていきます。
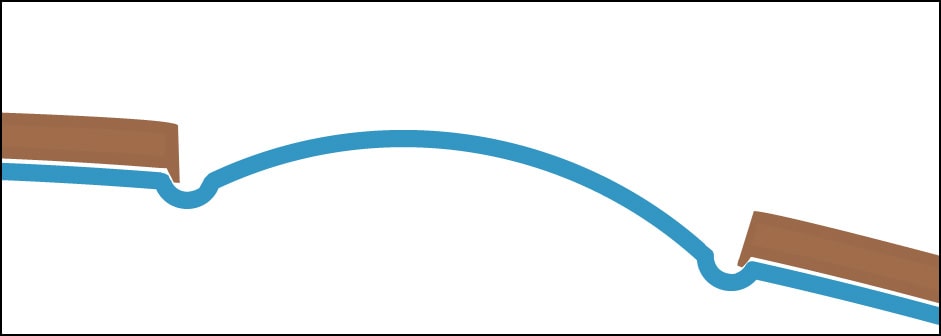
模様の部分を盛り上げ、加えて外周を溝で囲みます。まず、模様に凸をつけたことで切れ込みの目印ができます。盛り上がりの凸と溝の凹で立体感も増します。カバーの切れ込みは溝の側面途中で入れます。こうすることで、吹きこぼれたとしても表に出てくる部分を減らすことができます。
行う現場現場で色々と考え方はあるでしょうが、わたしは塗装のことを考えて原型にはかならずこれらのことを施します。
印刷合わせならば許されるかぎり凹凸はつけない。
印刷合わせによる着色は、先に印刷されたプラ板に成形をかけて模様付きの成形品を作りあげるということになります。加熱によって柔らかくなっているプラスチックを真空にて引っ張る。想像しただけでも印刷と形状がズレそうです。
印刷データーは事前に形状に合わせて作り直す。
お客様から頂く印刷原稿は、2DのXYのデーターです。立体用に使うために足りないZ部分を加えながらほぼ全て作り直します。
第十四回。【印刷成形のデーター作り】成形用に画像を作り直さないとちがう人になっちゃうよ。
・印刷データーを修正してもそれでもズレる。
かなりの時間をかけて、印刷成形用に頂いた原稿を修正します。しかし、本生産ではズレるものが出てきます。いや、全ての合い方が違うと言っても良いかもしれません。それを成形のガイドを直しながら、場合によっては型を動かしながら目立たないよう目立たないようしています。
・凹凸をつけずに印刷にて絵柄を表現する。
形状に凹凸をつけると言うことは、絵柄の形状や位置を確定するということになります。それは残念ながら、「ズレる部分を増やす」ということにもつながります。それゆえ、印刷で十分表現できるものはあえて形状に凹凸をつけません。
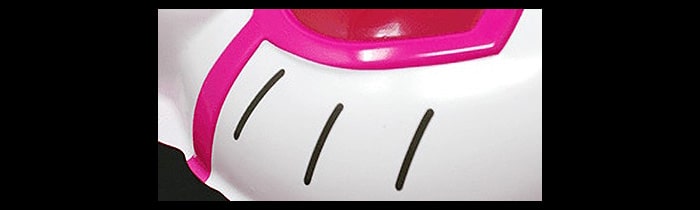
例えばこのお面。サングラスをつけているのですが、耳に掛けるテンプルに部分には凸はつけていません。ほおのヒゲも同様です。よくよく見ると、サングラスの縁の部分にズレが生じていることも分かります。
印刷合わせならば全体の高さも抑える。
今までは個々の凹凸に関してお話しましたが、全体の高さということも加えてお話します。
伸ばせば色が浅くなる。
お面の高さ(=厚み)に関して個人的な考えは「塗装ならば60-65㍉」「印刷合わせならば50㍉」を目安にしています。この数値の違いは何故なのでしょう?
・やはり高さを増せばズレやすくなる。
高さを増すということは「より伸ばす」ということです。つまり印刷と形状が合う条件をより困難にするということにつながります。
・色が浅くなる。
塗装の場合は、すでに形状確定したモノの上に色を乗せていくことになります。つまり、色が濃くなることはあっても作業前より色が薄くなることはありません。
それに対して印刷合わせの場合は、色が一番濃いのは成形前の平らな状態のときです。それ以降、成形で伸ばされれば伸ばされるほど、色は浅くなっていきます。と言って高さを抑え過ぎては立体のお面とは物足りなくなるので、経験的に50㍉としています。
原型は全ての始まり。
最初の工程ですから当たり前のことですが、ここまでお話したとおり、着色方法に沿った原型作りを行わないとその後の工程でそれはそれは大変な思いをすることになります。それは経験者のわたしが言うのだから間違いありません。(苦笑)
お面の製作、特に個人での製作や小ロットでの製作に関しては「できることはご自身でやって頂く」ことを推奨しています。前回、今回のお話が「お面の原型を自分で作る!」という皆様の参考になればと思います。
おめんギャラリー「#11 この素晴らしい仕上がり ‘tofuboy’お面。・・・正直、個人の方がここまでやるとは思わなかった。」
- 前の記事
第五十四回。EORA3D再挑戦。カタカタ音がしたので分解してみたが。やはり、iPhoneとBluetoothでつながらず 2020.08.17
- 次の記事
第五十六回。【パッケージ解体】さしてとめる カンミ堂「ペントネ(詰め替え用)」今日は紙製。 2020.08.26
コメントを書く