第四十九回。【おめんを語ろう・その3】原型編-1「基本的な考え」
-min.jpg)
お面の制作工程や、新規で発売される製品の話などを中心にお話して いく【お面を語ろう】
第三回目は、お面作りの最初の工程「原型を作る」上でのポイントという話です。 このポイントをお面作りならではの視点で説明しようと思います。
前回、着色の仕方によって作り方が変わってくるというお話をしました。彩色塗装なのか、印刷合わせで着色するのか。その選択による原型作りも変わってきます。そこまでは話すと長ーくなるので、今回はわたしが基本の基本と考えているところまでを。
第四十二回。【おめんを語ろう・その2】作り方は色の付け方で変わる。
原型は本当に重要
お面作りにおいてわたしが一番注意をはらうのは、この原型作りの工程かもしれません。
【原型確認はある意味、最初で最後の確認】
お面の初期準備はこのように進みます。
彩色塗装の場合ー原型→鋳物型→彩色カバー→抜型
印刷合わせの場合-原型→鋳物型→成形用印刷データー→印刷版→抜型
ご覧のとおり、どちらの製作方法とも原型がOKになった時点でその後の型類が作り始められます。逆を言えば、型類を作りあげて仕上がり見本を提出した後に形状の訂正が入ると全てがやり直しになるということです。
よくこういうお問い合わせを頂きます。「テスト品は出せますか?」「仕上がり見本はご提出しますが、たたき台のためのテスト品はお出ししていません」とわたしはお答えするようにしています。それは先程の理由からです。
原型がOKになれば、すべてがその形状に沿って動き出します。お客様との原型確認作業はある意味、最初で最後の確認だという気持ちでいつも行っていますし、そのように考えて頂いています。
【見映えと効率は原型で決まる】
真空成形品として不具合を起こさない形状設定は、どんな成形品においても大事です。型から外れる形状、しわを生じない形状このあたりは普通に考えることです。お面の製作過程においても、ここでよくよく考えないと後工程に大きな影響を与えてしまいます。
・重なりのよい形を考える
お面の製作には、「抜き」とか「開け」と言う工程が他の真空成形品に比べて多くあります。形状なりにカットする「外周抜き」、耳の穴(=ゴム紐穴)の「穴開け」はどんなお面にも必ず行われています。
目の穴に関しては印刷合わせで着色する場合には行わない場合がほとんどですが、彩色塗装の場合は必ず穴は開けています。ちなみに印刷合わせの場合は、透明の材料を使用してそこだけ印刷を入れずに目穴の代わりにするという方法が多くの場合で使われています。
わたしが工程を考える場合には、「抜き」も「開け」も成形品を重ねて作業できることを前提に考えます。つまり成形品を1枚1枚抜いたり開けたりするのではなく、2枚3枚重ねて行えるように形状を設定しておくということです。時間も費用もその分かかりません。
重ねをすることで大きなメリットが得られるお面だからこそ、原型を作る際には勾配や角Rをよくよく考慮して、「重なりのよい」形状を作っておく必要があります。重なりのよい型はある意味、離型性の良い型でもあります。
・しわを出さない
真空成形加工では「しわ」という現象をよく目にすると、以前話しました。
第十六回。真空成形でよくおきる現象【しわ】足りても出るし、足りなくても出るし。
「しわ」は見映えもよくありませんし、場合によってはそこから「割れ」が生じることもあります。どちらにしても、無いことに越したことはありません。
しわを取り除く方法に「プラグ」という補助具を使用するとも話しました。
お面の製作では、できればプラグは使いたくないものです。
プラグの使用によるしわ取りですが、取りづらい場合はどうしてもプラグを強く当てることになります。その場合、当てた痕=プラグ痕が残る場合があります。お面はお金を払って買ってもらう商品ですから、できればこのプラグ痕も残したくはない訳です。
また、印刷合わせでお面を作る場合。プラグという外部の力によって印刷の伸び方、つまり印刷と形の合わせが想定していたものと異なってしまう場合があります。
・彩色カバーがハマらない
プラグ痕に、印刷のズレ。それから忘れてはいけない理由がもう一つあります。彩色塗装に使う「マスキングカバー」との関係です。
彩色カバーはお面実物に銅電鋳を行って作られます。塗料に使われるシンナーに負けない銅製のお面に忠実な形状を持ったマスキングカバーです。そのため、電鋳に出したお面(マスター)にしわが生じていなければカバーにも当然その痕はありません。
それが本成形の途中からしわが生じ始めたとしたら。彩色カバーは被さりません。つまり塗装がうまく出来ず、最悪の場合、成形がやり直しになります。
カバーを作り直せばいいじゃないかと思われるかもしれません。しかし、しわはきっちり同じ位置に同じ形で出て来てくれる訳ではないので、カバーの作り直しは無意味なのです。
やはり原型の段階で「しわを出さない」形状を考慮しておくことが絶対だとわたしは思います。
・入り込んだところは作らない
入り込んだところとはこんな形状の部分です。
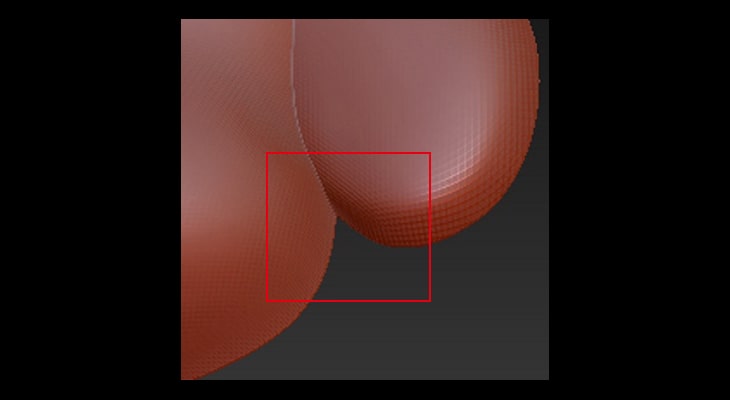
こういうところは強度が弱くなりがちです。前述の重ね抜き・開けの際や、数百枚をまとめて箱入れする時にこの部分がつぶれてしまうことがあります。それは見映えだけではなく、加工費用や梱包送料に大きな影響を与えますので要注意です。
この画像の原型はこの後、入り込みを直すべく大きなRをつけて完成まで持っていきました。
彩色塗装と印刷合わせの形状の表し方に大きな違いがある。この話は次回。
ここまで、お面の原型を作る際にわたしが気をつけている基本中の基本の話をしました。気をつけていても実際に成形をしてみると、想定に反したことが出てしまうことがあります。その時は苦肉の策で切り抜けますが、それでも初めに考えることで負担は軽くなっているはずです。
基本中の基本の話は、一般成形品にも通じる話でもありました。これからの話はお面ならではの話、「彩色塗装で着色をする時の原型作りの考え方」・「印刷合わせで着色をする時の原型作りの考え方」。これらの話はそこそこボリュームがありますので次回にということにしたいと思います。
- 前の記事
第四十八回。台紙や外箱の印刷で目を奪う ひとくふう。 2020.07.29
- 次の記事
第五十回。【パッケージ解体】1967年 ‘大きいことはいいことだ’ 2020年 ソフト99「サンドキューブ」‘小さいことはいいことなんだ’ 2020.08.01
コメントを書く